Prismatic Cell Sealing refers to the process of ensuring that prismatic lithium-ion battery cells are properly sealed to prevent leakage, contamination, and environmental exposure. Prismatic cells, unlike cylindrical or pouch cells, have a rectangular shape with flat sides, making them ideal for applications where space optimization and structural rigidity are important, such as in electric vehicles (EVs), energy storage systems, and consumer electronics.
Proper sealing is critical for the performance, safety, and longevity of prismatic cells. Below is an overview of the key aspects of prismatic cell sealing.
---
●Importance of Prismatic Cell Sealing
1. Leak Prevention:
- Prevents electrolyte leakage, which can cause short circuits, reduced capacity, or even thermal runaway.
2. Environmental Protection:
- Protects the internal components of the cell from moisture, dust, and other contaminants that could degrade performance.
3. Safety:
- Ensures the cell remains intact under mechanical stress, vibration, or pressure changes during operation.
4. Longevity:
- Maintains the integrity of the cell over its lifecycle, ensuring consistent performance and reliability.
---
●Components Involved in Sealing
1. Case/Enclosure:
- The outer casing of the prismatic cell is typically made of aluminum or steel, providing structural support and protection.
2. Sealing Gasket:
- A gasket or sealant material (e.g., rubber, silicone, or polymer-based) is used to create a tight seal between the case and lid.
3. Lid/Cover:
- The lid is welded or bolted onto the case to form a hermetic seal.
4. Terminal Feedthroughs:
- Electrical terminals must pass through the sealed enclosure without compromising the seal. Insulating materials are used to isolate the terminals while maintaining the seal.
5. Valve Mechanism:
- Some prismatic cells include safety valves to release excess pressure in case of overcharging or thermal events.
---
●Sealing Techniques
1. Welding:
- Laser Welding: Provides precise and strong seals, commonly used for joining metal parts.
- Resistance Welding: Used for smaller components or when laser welding is not feasible.
2. Adhesive Bonding:
- Specialized adhesives or epoxies are applied to bond the lid and case together. This method is less common due to concerns about long-term durability.
3. Gasket Sealing:
- A gasket is placed between the case and lid to create a compression seal. Materials like silicone, EPDM (ethylene propylene diene monomer), or FKM (fluorocarbon rubber) are often used.
4. Crimping:
- The edges of the case and lid are crimped together to form a mechanical seal. This method is sometimes combined with adhesive bonding for added security.
5. Hermetic Sealing:
- Involves creating an airtight seal using techniques like glass-to-metal sealing or metal-to-metal welding. This is essential for high-reliability applications.
---
●Quality Control in Sealing
1. Leak Testing:
- Methods like helium leak testing or vacuum decay testing are used to verify the integrity of the seal.
2. Visual Inspection:
- Ensures there are no visible defects in the welds, gaskets, or other sealing components.
3. Pressure Testing:
- The cell is subjected to internal or external pressure to check for leaks or deformation.
4. Environmental Testing:
- Simulates real-world conditions (e.g., temperature cycling, humidity, vibration) to assess the long-term stability of the seal.
---
Li Ion Battery Making Machine
●Challenges in Prismatic Cell Sealing
1. Material Compatibility:
- The sealing materials must be compatible with the cell's electrolyte and other chemicals to avoid degradation.
2. Thermal Management:
- Seals must withstand temperature fluctuations without losing their effectiveness.
3. Mechanical Stress:
- Vibration, impact, and pressure changes during operation can compromise the seal if not properly designed.
4. Cost and Complexity:
- Advanced sealing techniques and materials can increase manufacturing costs and complexity.
---
●Advances in Sealing Technology
1. Advanced Materials:
- New polymers and composites are being developed to improve seal durability and chemical resistance.
2. Automation:
- Automated welding and assembly processes enhance consistency and reduce human error.
3. Smart Seals:
- Incorporating sensors into the seal to monitor its condition and provide early warnings of potential failures.
4. Sustainability:
- Research is ongoing to develop recyclable or environmentally friendly sealing materials.
---
●Applications of Prismatic Cell Sealing
1. Electric Vehicles (EVs):
- Prismatic cells are widely used in EV batteries due to their high energy density and structural rigidity.
2. Energy Storage Systems (ESS):
- Used in stationary energy storage applications for grid stabilization and backup power.
3. Consumer Electronics:
- Found in laptops, tablets, and other devices where space efficiency is important.
4. Industrial Equipment:
- Powers tools, machinery, and other equipment requiring reliable and durable battery solutions.
---
●Conclusion
Prismatic cell sealing is a critical aspect of battery manufacturing that directly impacts the performance, safety, and lifespan of the cell. By employing advanced sealing techniques and materials, manufacturers can ensure that prismatic cells meet the demanding requirements of modern applications. As battery technology continues to evolve, innovations in sealing will play a key role in improving the reliability and sustainability of lithium-ion batteries.
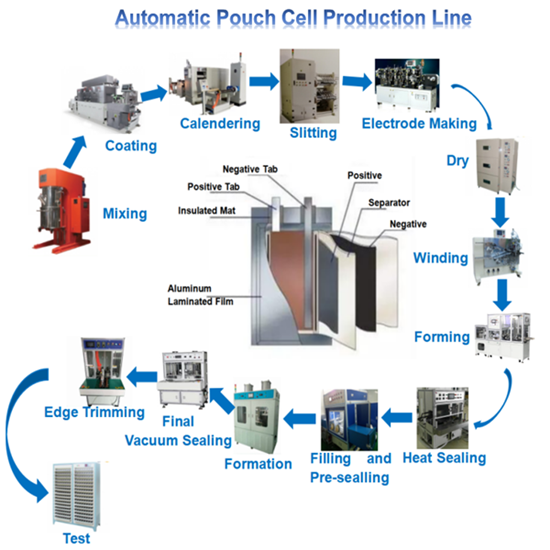